What is Deaerator?
Deaerator is a mechanical equipment that removes dissolved gases mainly dissolved oxygen & other non-condensable gases from boiler feed water. Oxygen causes pitting type corrosion in feed water systems. The process of removing dissolved gases from water also known as mechanical Deaeration.
Deaeration process of boiler feed water divided in two parts:
- Mechanical Deaeration
- Chemical Deaeration
Mechanical Deaeration considered as a first stage process where most of the dissolved gases are escaped from water. On the other hand chemical Deaeration is acts as a polishing process which can remove trace amount of dissolved gases by adding proper oxygen scavenger chemicals in deaerator.
Deaerator Working Principle:
Basically, Deaerator works based on two gas law.
- Henry’s Law (scrubbing with oxygen free steam): The amount of dissolved gases present in water is directly proportional to the partial pressure of that gas in the vapor space above the water/gas interface.
- Charles’ Law (oxygen solubility vs temperature): The solubility of oxygen decreases as the temperature of water increases.
Thus, we can remove dissolved gas from water by reducing the partial pressure of that gas in the atmosphere where it is contacting the liquid. You can accomplish this situation in deaerator by introducing a new gas, so that unwanted gas vented out.
Temperature is also a very important factor. The rate of diffusion of gas molecules also increases as the temperature increases.
Why steam is used as a purge gas in deaerator?
- It doesn’t contaminate the water.
- Only a small quantity of steam is venting from deaerator. Most of the steam condenses and becomes the part of deaerated water.
- It heats the boiler feed water up to the saturation temperature so that solubility of unwanted dissolved gases are decreases.
How Does a Deaerator Work?
Deaeration process in deaerator accomplished in two simple steps:
- First Step: Water is heated by steam within a few degree of its saturation temperature according to deaerator’s operating pressure. Approx. 97-98% of dissolved gases released with the steam & escaped from the vents of deaerators.
- Second Step: Remainder 2-3% of dissolved gases removed by scrubbing the water with the steam & addition of oxygen scavenger chemicals.
Venting is critical and necessary for the effective removal of dissolved gases like oxygen and other non-condensable gases such as carbon dioxide.
The vendors of deaerators usually gives guarantee of less than 7 ppb of dissolved oxygen in boiler feed water.
Solubility of Oxygen in Water:
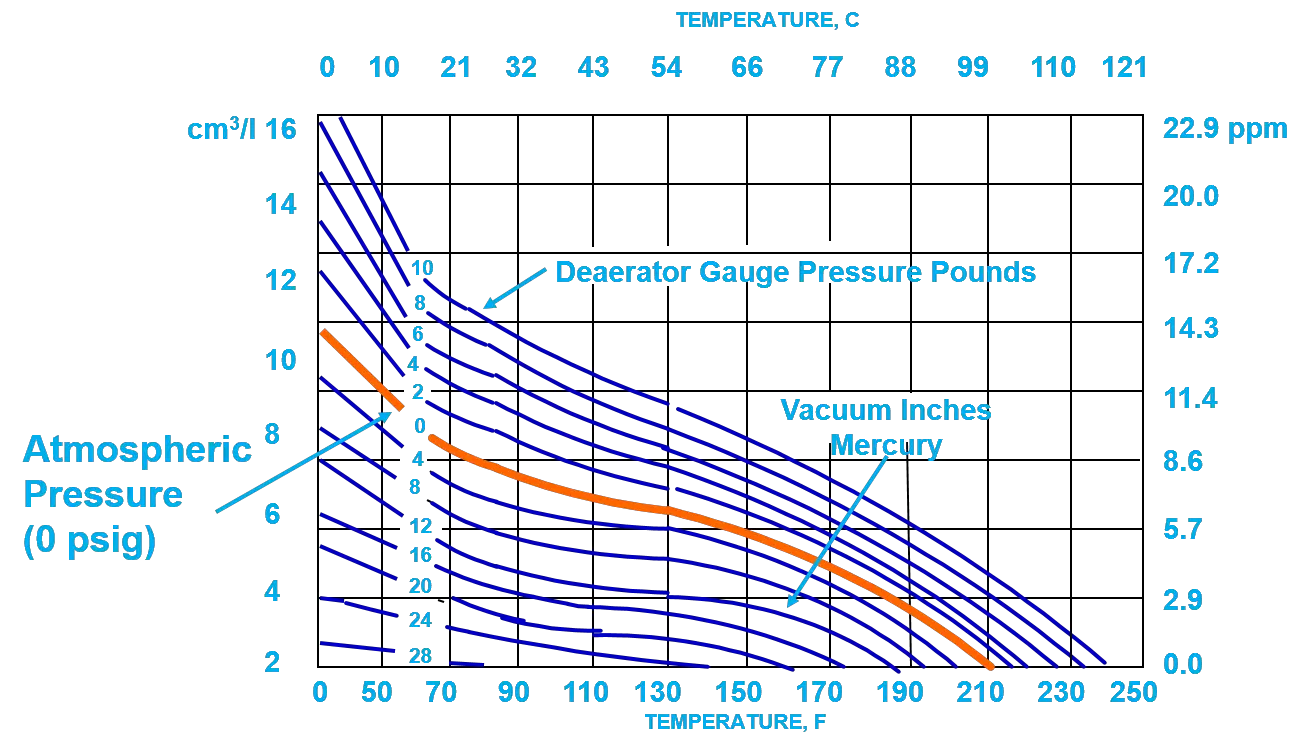
Types of Deaerators:
There are major three types of deaerator used in the industries are:
1. Vacuum Deaerators:
- Reduce partial pressure which reduces oxygen solubility
- Remove gases by creating vacuum
- Saturation temperature is achieved by reducing pressure
- Enlarge contact surface by water spraying and film formation
- Not as efficient as steam deaerators in terms of dissolved oxygen
- Typical oxygen level found are 200 -300 ppb(0.2-0.3 ppm)
2. Hotwells & Open Heaters:
- Primarily seen in low pressure boilers
- Non-pressurized vessel or tank where cold, oxygenated make-up water and hot condensate are mixed
- Feed water tank should be steam sparged
- Dissolved oxygen level normally found around 0.5 – 3.0 ppm. It depends on % make-up, steam-sparge, temperature & vent rate
3. Pressure Deaerators:
This type of deaerators are most efficient & used in all the power plants.
Operating Principles:
- Formation of fine water droplets by spray nozzles(Henry’s law)
- Steam heats the fine water droplets near to saturation temperature(Charles’ law)
- Mechanical scrubbing of dissolved oxygen and other non-condensible gases from droplets by oxygen-free steam
- Finally, Venting of oxygen-rich steam to atmosphere & replacement with fresh, O2-free steam
Benefits of Pressure Deaerators:
- Most efficient method of dissolved oxygen reduction
- Capable for reduction of all non-condensable gases including carbon dioxide
- Improves thermal efficiency of plant
- Provide feed water storage capacity
Types of Pressure Deaerators:
- Spray type
- Tray type
Let’s discuss both types of deaerator in detail:
Spray Type Deaerator:
Spray deaerator is generally a single vessel with either vertical or horizontal arrangements. Deaeration process & storage both work are done in single vessel.
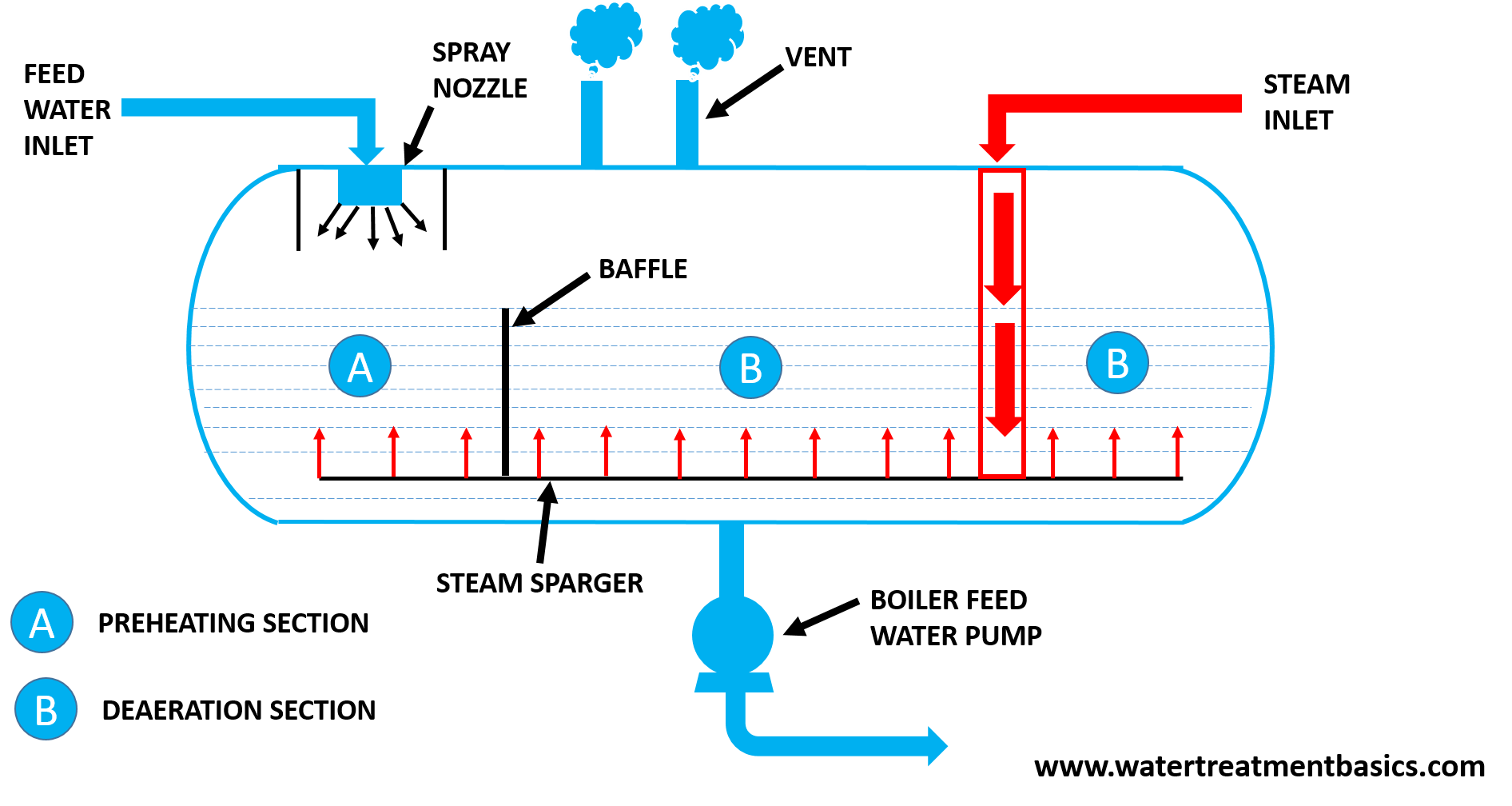
Spray deaerator consist of horizontal vessel (see above figure) & which has two sections namely preheating section and Deaeration section. Both the sections are separated by a baffle.
Boiler feed water sprayed from top through spray nozzles and it is preheated by steam which is coming from sparger. The purpose of the pre heating is to raise the temperature of feed water to its saturation temp at deaerator operating pressure.
The preheated feedwater then flows into the deaeration section, where it is deaerated by the steam rising from the sparger system.
The dissolved gases stripped out from the water & exit via vent which is available at top of the vessel.
Finally, Deaerated boiler feed water is pumped to the boiler through boiler feed water pump (BFP) from the bottom of the vessel.
Tray Type Deaerator:
The tray type deaerator is also known as cascade type deaerator. This type of deaerator consists of two vessels. Horizontal vessel mounted above the vertical vessel.
Horizontal vessel which acts as a Deaeration section & vertical vessel which stores the deaerated boiler feed water.
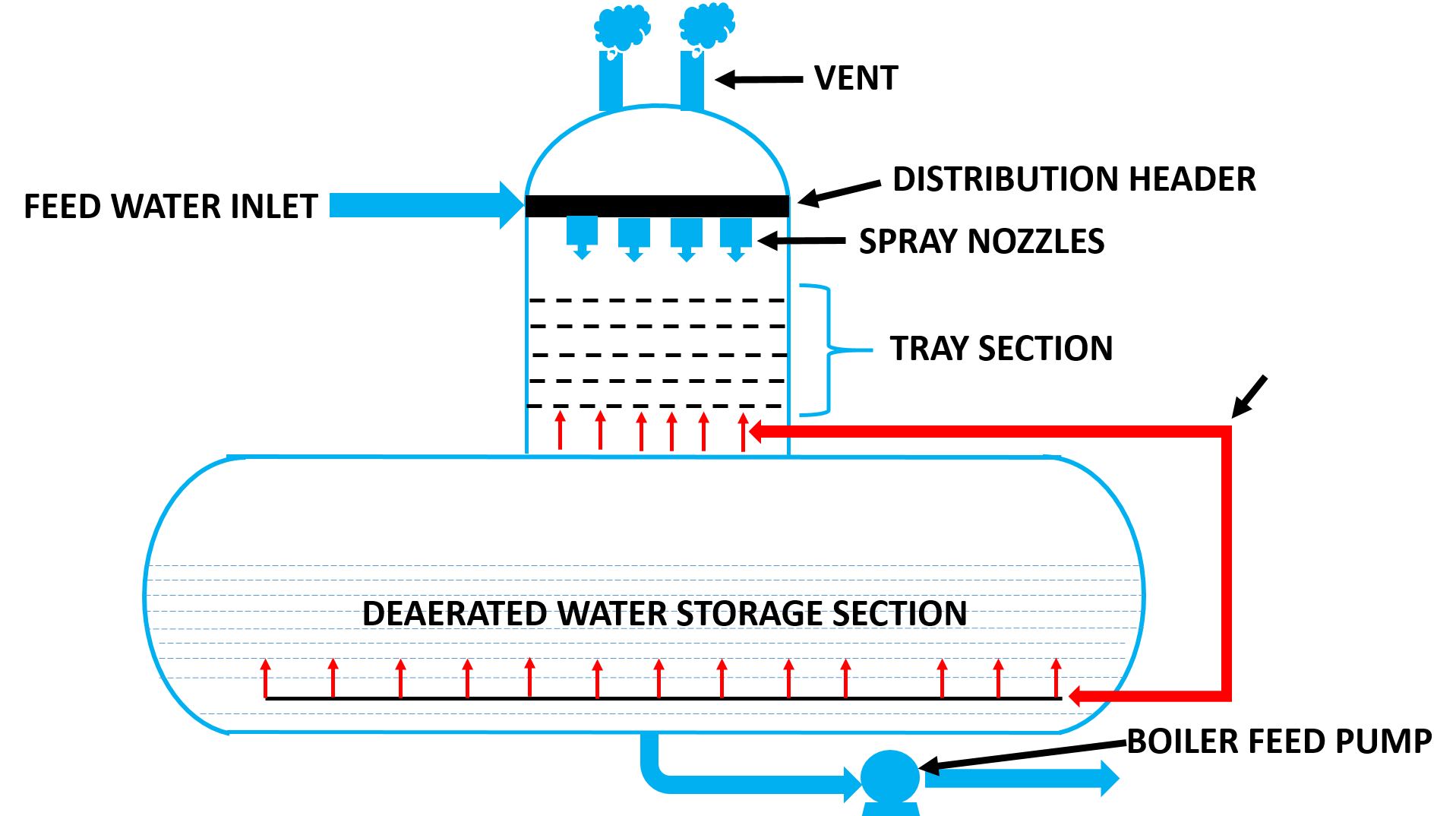
Boiler feed water first enters into the vertical vessel which has a perforated trays & flows down wards through perforations. Low pressure steam enters below the perforated tray & flow upwards. This arrangement provides better contact & mixing of steam with boiler water.
Steam stripped out the dissolved gases from boiler feed water & these gases are exit out via vents which is given at top of the horizontal vessel. Horizontal vessel also has a sparger system which keep boiler feed water warm.
Finally, treated deaerated boiler feed water sent to the boiler via boiler feed pump.
Typical Arrangement of deaerator units:
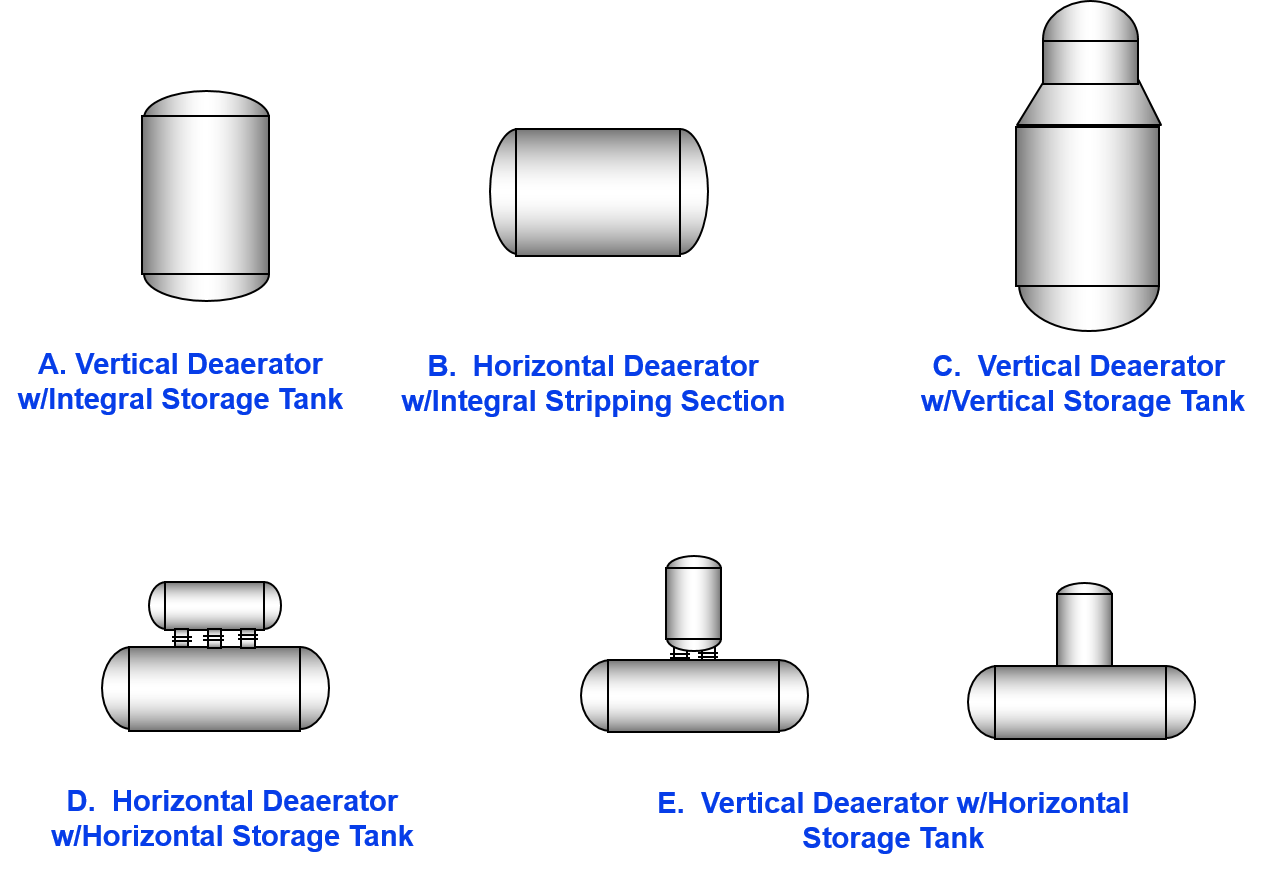
Deaerator Pressure and Temperature (Performance Guidelines):
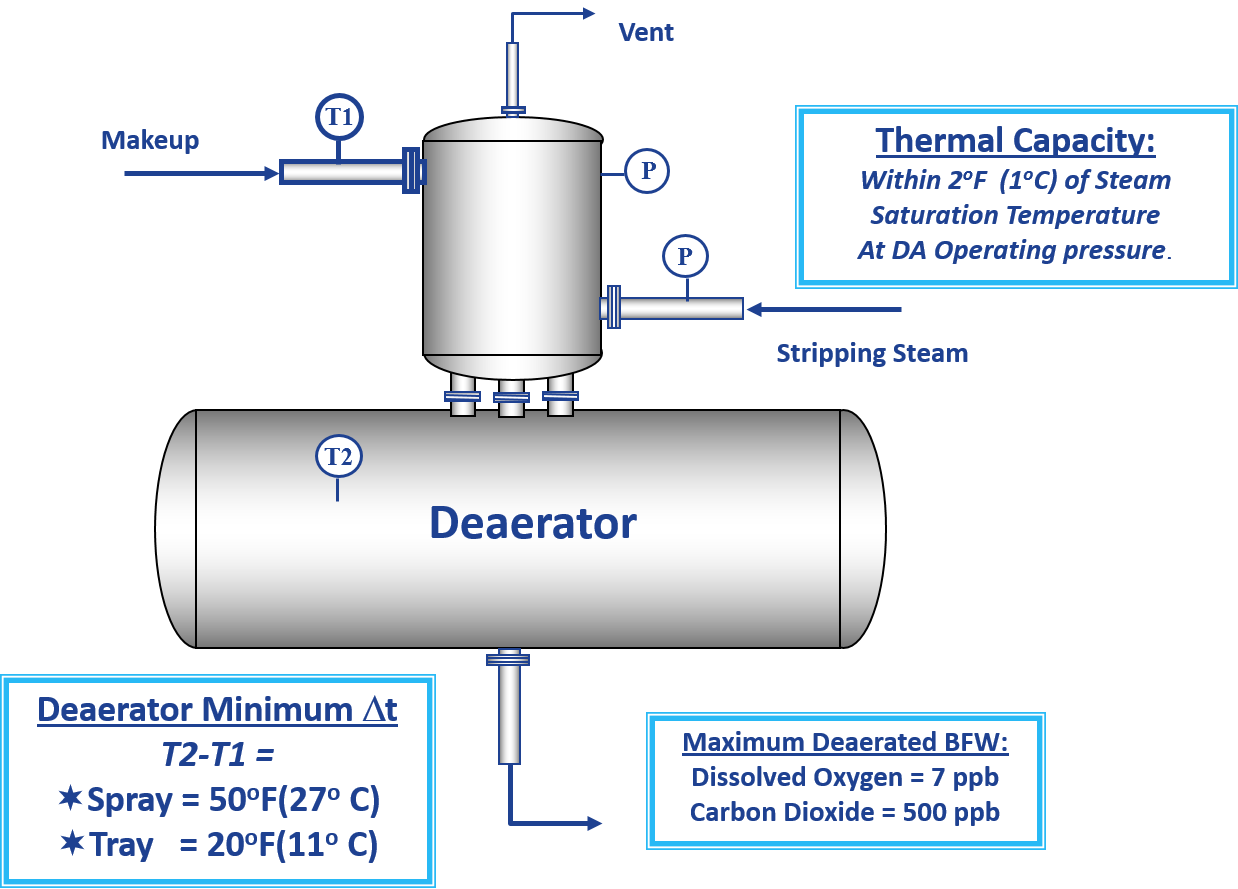
Deaerator Steam Requirement Calculation:
The amount of steam required to heat and deaerate the makeup water including vented steam, depends on the amount of incoming water and its temperature.
Generally, the inlet feed water temperature must be at least 20deg F(11 deg C) below the deaerator steam temperature for proper Deaeration in spray-tray design and upto 50 deg F(27 deg C) in spray only design.
The approximate steam flow required is a minimum of 1% of the inlet feed water flow for each 10 deg F or 7 deg C temperature rises across the deaerator.
Deaerator Vent:
The vent valve should not be operated in a closed position. Normally, the valve should be open one or more turns to allow for complete removal of the gasses. To determine the correct amount of opening required, the vent valve should be opened approximately one or two turns and the effect on the temperature noted.
If no appreciable effect on the temperature is noted after a period of one hour, oxygen tests should then be made to determine the effectiveness of venting; satisfactory reduction of oxygen is obtained when tested by a recognized sampling and testing procedure.The vent setting of the valve can be further decreased by tightening the vent valve.

Normally, the plume of steam would indicate sufficient venting if it appears firm and rises approximately 18 inch to 36 inch above the pipe.
If after reducing the vent valve openings a drop in operating temperature is observed, or a difference between outlet temperature of the water in comparison with the saturated temperature of the steam is observed, then the venting is not adequate and the vent valve or orifice must be opened further.
Key Takeaways:
- Two types of pressure deaerators – Spray Type and Tray Type (Spray-Tray Type)
- All pressure DA’s have spray nozles
- Tray type are more efficient
- Manufacturers are typically guaranteed for <7 ppb dissolved oxygen in deaerator outlet water without feeding of oxygen scavenger chemical
Deaerator Performence Issues:
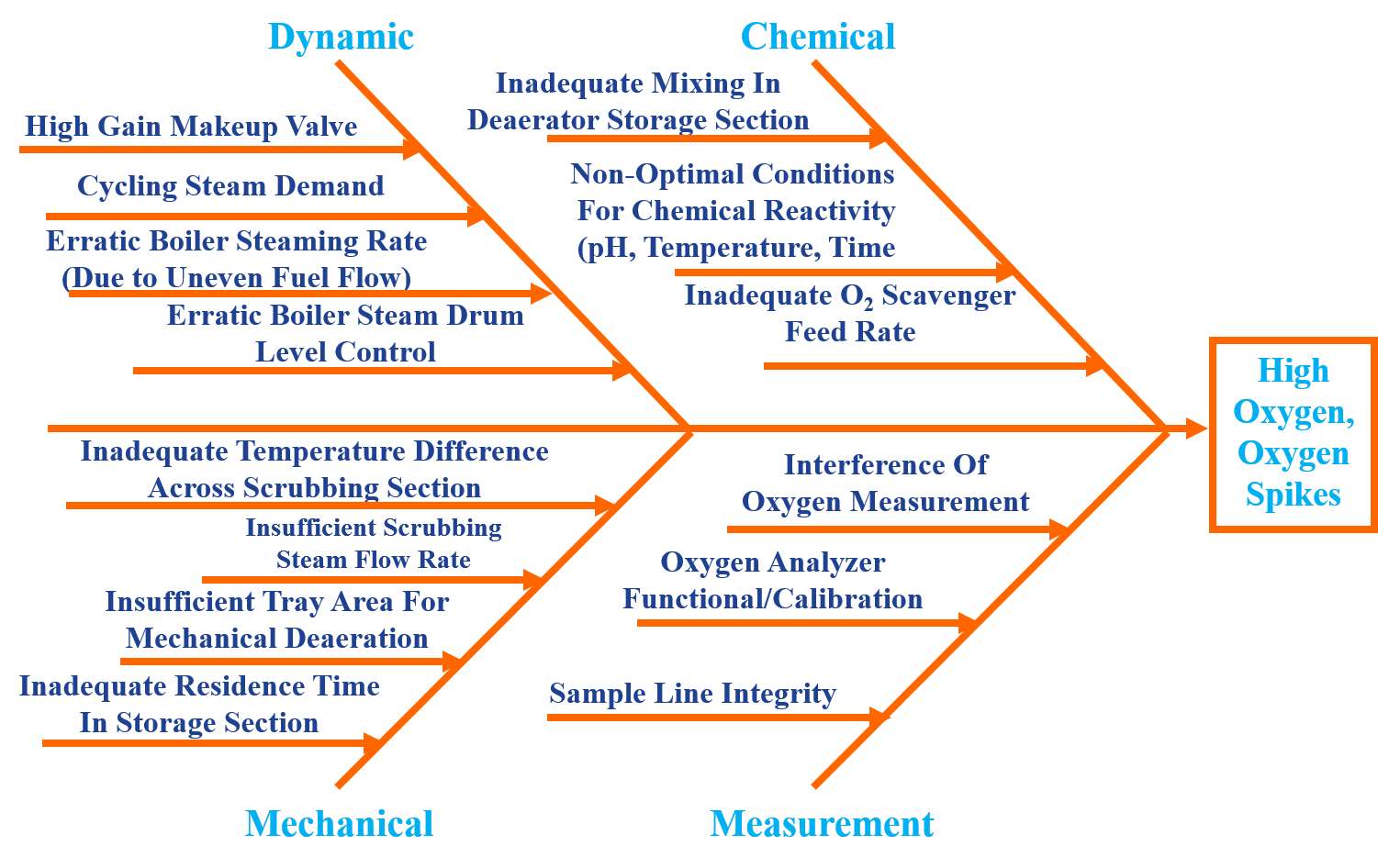
In Conclusion, Deaerator is very important equipment for boiler feed water treatment. It can improve the the life of BFW system & also improve the performence of the plant. Dissolved oxygen level should monitor in deaerator outlet water on daily basis to check the performence of it.
Why Deaerator is Placed At Height?
Deaerator placed at height because it provides required NPSH(Net Positive Suction Head) for boiler feed pump to avoid cavitation at the suction of boiler feed pump.
How To Check The Deaerator Venting is Proper?
Deaerator vent should be constant & rises 18 inch to 36 inch above the pipe.